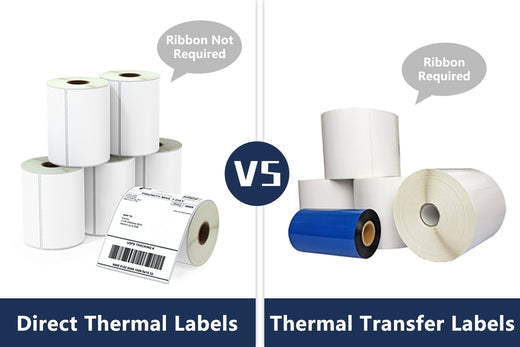
Direct Thermal Labels Vs. Thermal Transfer Labels
|
|
Time to read 4 min
Written by: Beichen Lu
|
|
Time to read 4 min
Many of our customers have been asking about the difference between direct thermal labels and thermal transfer labels. This blog is here to help you understand the distinctions between these two types of labels and printing methods. We'll break down the details to make it easy for you to choose the labels that suit your needs best.
Table of Content
In the process of direct thermal printing, the tiny heat-emitting parts of the print head apply focused heat directly onto the label as it moves by. This label is coated with a heat-sensitive layer. Through a chemical reaction, the label transforms its color from white to black.
In thermal transfer printing, the heat-producing components of the print head apply precise heat to the moving ribbon. This heat melts the ribbon onto the label's surface, shaping the printed image. The label absorbs the ink, making it an integral part of the material. It's important to ensure that the ribbon and label stock (including material and adhesive) are a suitable match for both each other and the intended use. This ensures the best possible quality and resilience for your printing needs.
The images created on direct thermal labels are typically more vulnerable to external factors like sunlight. They can lose their color, aka fade, over time and are better suited for shorter-term uses.
Because of these factors, direct thermal printing isn't the ideal option for extended periods. However, it's important to note that direct thermal printing still offers a satisfactory lifespan for many purposes.
Thermal transfer labels commonly exhibit greater sturdiness and resilience against external influences. The printed images on these labels are less prone to fading, rendering them particularly suitable for scenarios where lastingness is of significance.
This method is well-suited for prolonged applications that extend beyond six months or encompass challenging conditions like chemicals, intense light, elevated temperatures, or moisture exposure. As a result, thermal transfer printing is excellently tailored for tasks such as tracking assets, handling laboratory samples and blood pouches, outdoor applications, establishing permanent identification, and maintaining legibility in cold and freezer storage environments.
These labels usually present a more budget-friendly option from the start, as they don't necessitate extra supplies like ribbons.
Direct thermal printers, sans the requirement for ribbons, boast simplicity in operation and entail fewer components prone to malfunction. Typically, these printers come with a lower initial cost and demand less ongoing upkeep and repair compared to thermal transfer printers. While direct thermal labels might have a slightly higher price tag, you can avoid expenditure on ribbons.
Thinking about printing with thermal transfer labels involves using ribbons, which adds to the starting cost when you buy printers and the ongoing cost when you buy ribbons. This can make your overall expenses higher.
Some thermal transfer printers can also work in a direct thermal mode without needing ribbons. This could be helpful for small businesses that want more options without dealing with the trouble or extra expense of having multiple printers.
Direct thermal labels are employed in various fields because they offer good quality printing and are simple to use. Here are some common uses of direct thermal labels:
These uses showcase the convenience and effectiveness of direct thermal labels across different tasks.
Because they are very strong and can withstand tough situations, thermal transfer labels are used for labeling things for a long time and in really tough conditions. Here are some ways these labels are commonly used:
The most important things to think about when choosing between the two technologies are:
Direct thermal printers are good for things you only need to label for a short time (less than six months). On the other hand, thermal transfer printers work better if you want the label to last a long time (more than six months) or if it will be outside a lot or in tough conditions.
Because both direct thermal and thermal transfer printing have their own good and bad points, they will both keep being used for different things in a company. For example, thermal transfer printers might be used to mark products right when they're made, while direct thermal printers might still be the best choice for making labels for picking items and shipping them.
If you want to buy thermal labels or sticker paper, you can check out more on our store
Products Featured In This Blog
24/7 support team
Multiple Payment Methods
Worry-free shopping
Delivery in 3-7 business days
Be the first to know about label discounts,
product launches, and time-saving tips — subscribe now!
Are you 18 years old or older?
Sorry, the content of this store can't be seen by a younger audience. Come back when you're older.
Dymo 30299 Compatible Jewelry Price Tag 2-up Barbell Labels 3/8" x 3/4
I have bought many of these labels over the years without a single glitch in performance. I run them on a ZP 505 and have no issues whatsoever.
These labels are great quality. I only needed a few of this size and happy I did not have to buy a case!
so far they work great, quick shipping and no minimum qty
The labels are always exactly what we need. They are great quality and work specifically for our needs. Thank you for having these.